APQP (geavanceerde productkwaliteitsplanning)
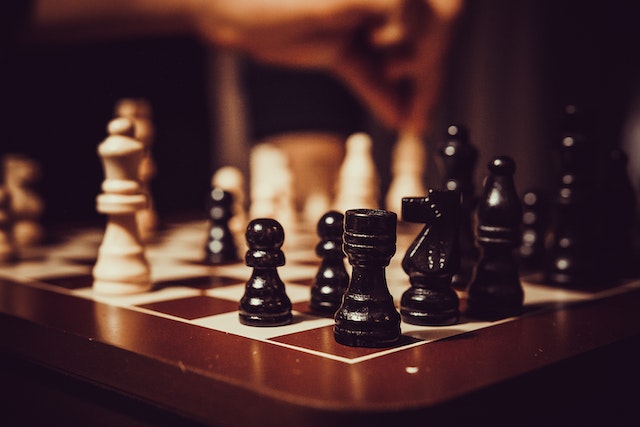
- 1564
- 312
- Glen Armstrong
Wat is de APQP?
APQP (geavanceerde productkwaliteitsplanning), In het Spaans "geavanceerde productkwaliteitsplanning", is een kader van procedures en technieken die worden gebruikt om producten in de industrie te ontwikkelen, met name in de automobiel.
Complexe leveringsproducten en ketens hebben veel mogelijkheden om te falen, vooral wanneer nieuwe producten worden gelanceerd. APQP is een gestructureerd proces voor het ontwerpen van producten en processen, gericht op het garanderen van klanttevredenheid met nieuwe producten of processen.
Deze aanpak maakt gebruik van tools en methoden om de risico's die verband houden met veranderingen in een nieuw product of proces te verminderen.
Het doel is om een gestandaardiseerd plan voor productkwaliteitseisen te produceren, waardoor leveranciers een ontwerp kunnen worden dat de klant tevreden stelt, waardoor communicatie en samenwerking tussen verschillende activiteiten wordt vergemakkelijkt.
In het APQP -proces wordt een multifunctionele apparatuur gebruikt, die marketing, productontwerp, aankopen, productie en distributie omvat. Dit proces wordt gebruikt door General Motors, Ford, Chrysler en hun leveranciers, voor zijn productontwikkelingssysteem.
APQP -fasen
APQP dient als een gids in het ontwikkelingsproces en ook als een standaard manier om resultaten te delen tussen leveranciers en autobedrijven. Het bestaat uit vijf fasen:
Fase 1: Planning en definitie van het programma
Wanneer de vraag van de klant de introductie van een nieuw product of de beoordeling van een bestaande vereist, wordt planning een centraal thema, zelfs vóór de discussies over het ontwerp of het herontwerp van het product.
In deze fase wil planning de behoeften van de klant en ook de verwachtingen van het product begrijpen.
Planningactiviteiten omvatten het verzamelen van de benodigde gegevens om te bepalen wat de klant wil en vervolgens deze informatie te gebruiken om de productkenmerken te bespreken.
Kan u van dienst zijn: primaire sector: kenmerken, economische activiteiten, belangVervolgens kunt u het kwaliteitsprogramma definiëren dat nodig is om het product te maken zoals gespecificeerd. Het resultaat van dit werk omvat productontwerp, betrouwbaarheid en kwaliteitsdoelstellingen.
Fase 2: Productontwerp en -ontwikkeling
Het doel van deze fase is om het productontwerp te voltooien. Hier is ook een evaluatie van de levensvatbaarheid van het product. De resultaten van werk in deze fase zijn onder meer:
- Beoordeling en verificatie van het voltooide ontwerp.
- Gedefinieerde specificaties van materialen en vereisten van apparatuur.
- Effectanalyse en ontwerpfoutmodus voltooid om de kans op fout te evalueren.
- Controleplannen vastgesteld voor het maken van het productprototype.
Fase 3: Ontwerp en ontwikkeling van het productproductieproces
Deze fase richt zich op de planning van het productieproces dat het nieuwe of verbeterde product zal produceren.
Het doel is om het productieproces te ontwerpen en te ontwikkelen, rekening houdend met de specificaties en productkwaliteit en productiekosten.
Het proces moet in staat zijn om de nodige bedragen te produceren om aan de verwachte vraag van consumenten te voldoen, terwijl de efficiëntie wordt gehandhaafd. De resultaten in deze fase zijn onder meer:
- Een volledige processtroomconfiguratie.
- Een effect- en faalanalyse van het volledige proces om risico's te identificeren en te beheren.
- Kwaliteitsspecificaties van het bedrijfsproces.
- Productverpakkingen en afwerkingsvereisten.
Fase 4: Proces- en productvalidatie
Het is de testfase om het productieproces en het eindproduct te valideren. De stappen omvatten:
- Bevestiging van de capaciteit en betrouwbaarheid van het productieproces. Evenzo is het criterium voor het accepteren van productkwaliteit.
Kan u van dienst zijn: eenvoudige interesse: elementen, hoe het te berekenen en voorbeeld- Realisatie van testproductieruns.
- Producttest om de effectiviteit van de geïmplementeerde productiebenadering te bevestigen.
- Akkoord met de nodige aanpassingen voordat u doorgaat naar de volgende fase.
Fase 5: lancering, evaluaties en continue verbetering
In deze fase treedt de lancering van grootschalige productie op en benadrukt het om de processen te evalueren en te verbeteren.
Onder de pijlers van deze fase zijn de vermindering van procesvariaties, de identificatie van problemen en het begin van corrigerende acties om continue verbetering te ondersteunen.
Er zijn ook het verzamelen en evalueren van feedback van klanten en gegevens met betrekking tot de efficiëntie van het proces en de kwaliteitsplanning. De resultaten omvatten:
- Een beter productieproces, door procesvariaties te verminderen.
- Kwaliteitsverbetering in productbezorging en klantenservice.
- Verbetering van de klanttevredenheid.
Voorbeeld
Waar APQP op te nemen
- Ontwikkeling van vereisten van de stem van de klant, met behulp van de implementatie van de kwaliteitsfunctie.
- Ontwikkeling van een productkwaliteitsplan geïntegreerd in het projectschema.
- Productontwerpactiviteiten die speciale of belangrijke kenmerken communiceren om ontwerpactiviteit te verwerken, voordat het ontwerp wordt bevrijd. Dit omvat nieuwe vormen en onderdelen, meer strakke toleranties en nieuwe materialen.
- Ontwikkeling van proefplannen.
- Gebruik van formele ontwerpbeoordeling om de voortgang te controleren.
- Planning, acquisitie en installatie van geschikte apparatuur en gereedschappen, volgens ontwerptoleranties gegeven door de productontwerpbron.
Kan u van dienst zijn: Economische instellingen: kenmerken, voorbeelden, doelstellingen- Suggestie communicatie door assemblage- en productiepersoneel over de manieren om een product beter te assembleren.
- Het opzetten van geschikte kwaliteitscontroles voor speciale kenmerken of sleutels van een product of parameters van een proces, die nog steeds het risico lopen op potentiële mislukkingen.
- Stabiliteitsstudies en capaciteit van speciale kenmerken uitvoeren om de huidige variatie te begrijpen en dus toekomstige prestaties te voorspellen met statistische procescontrole en procescapaciteit.
Industrieën die het gebruiken
Ford Motor Company publiceerde in de vroege jaren 80 de eerste geavanceerde kwaliteitsplanninghandleiding voor zijn leveranciers. Dit hielp Ford -leveranciers om voldoende controles te ontwikkelen voor de preventie en detectie van nieuwe producten, waardoor de kwaliteit van de bedrijfskwaliteit werd ondersteund.
Aan het einde van de jaren 80 gebruikten de belangrijkste fabrikanten van de auto -industrie in de Verenigde Staten APQ -programma's. General Motors, Ford en Chrysler hadden het geïmplementeerd en zagen vervolgens de noodzaak om mee te doen om voor hun leveranciers een gemeenschappelijke kern van de principes van de productkwaliteit te creëren.
De richtlijnen werden in de vroege jaren 90 vastgesteld om ervoor te zorgen dat APQP -protocollen doorgaan met een gestandaardiseerd formaat.
De vertegenwoordigers van de drie autofabrikanten en de American Society for Quality Control creëerden een groep kwaliteitsvereisten, om een gemeenschappelijk begrip te hebben van kwesties van wederzijds belang binnen de auto -industrie.
Deze methodologie wordt nu ook door progressieve bedrijven gebruikt om kwaliteit en prestaties te garanderen door middel van planning.
Referenties
- Geavanceerde Product Kwaliteit Planning. Uit NPD-oplossingen genomen.com.
- Geavanceerde productkwaliteitsplanning (APQP). Uit kwaliteit genomen.com.